One of J.C. Newman’s historic brands, Sarzedas was known as “The Aromatic Cigar.” U.S. Patent Office records show that J.C. Newman first rolled Sarzedas cigars in 1900. A century ago, Sarzedas was widely known as “The Aromatic Cigar.” One hundred and...
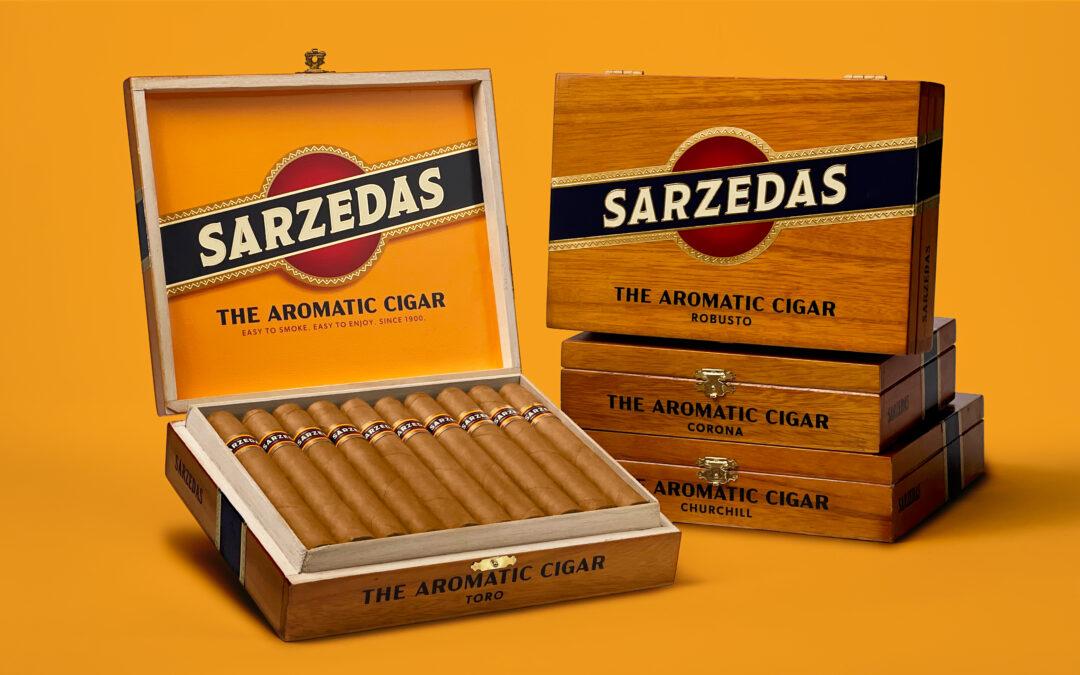
J.C. Newman Introduces Sarzedas, a New Nicaraguan Brand
One of J.C. Newman’s historic brands, Sarzedas was known as
“The Aromatic Cigar.”
U.S. Patent Office records show that J.C. Newman first rolled Sarzedas cigars in 1900. A century ago, Sarzedas was widely known as “The Aromatic Cigar.” One hundred and twenty-five years later, J.C. Newman will reintroduce Sarzedas cigars at the Premium Cigar Association Trade Show in New Orleans this weekend. The new Sarzedas cigars are handmade at J.C. Newman’s PENSA cigar factory in Esteli, Nicaragua.
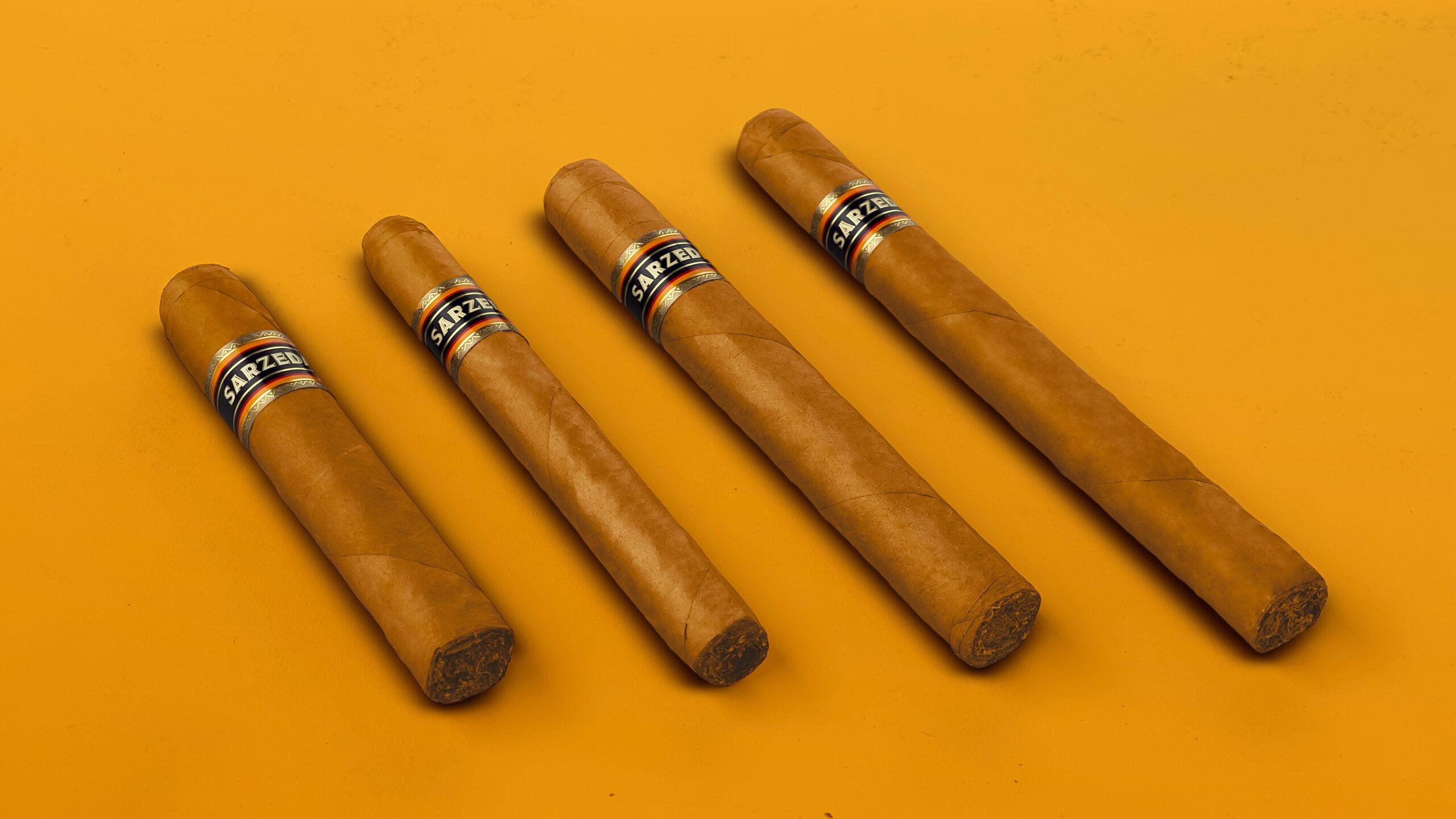
“I have loved the Sarzedas name and the brand’s history as ‘The Aromatic Cigar’ for years,” said fourth-generation owner Drew Newman. “I have been wanting to bring this historic brand back, but had to wait until we could create a blend that lives up to the brand’s legacy. Sarzedas is the most flavorful cigar we have ever made.”
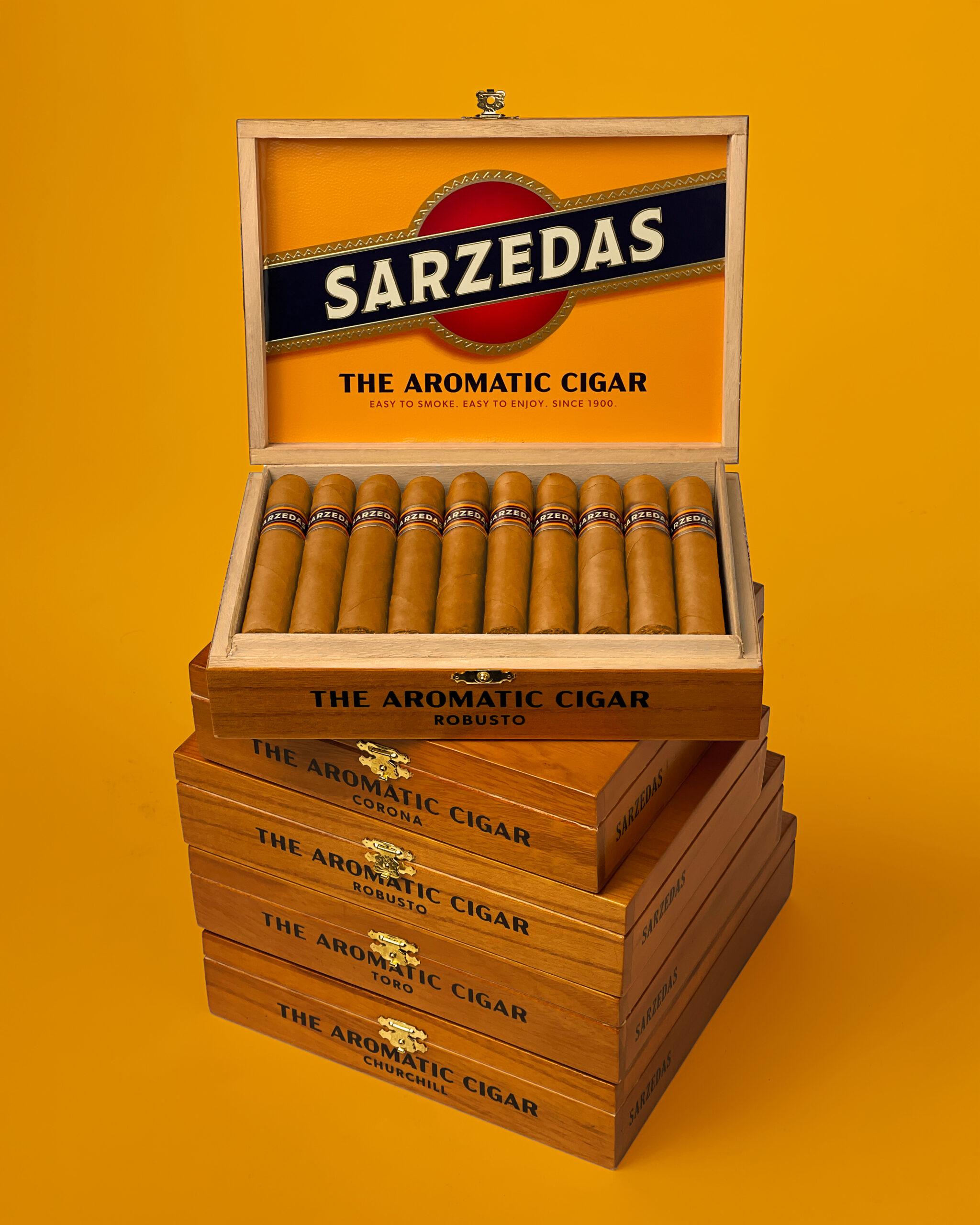
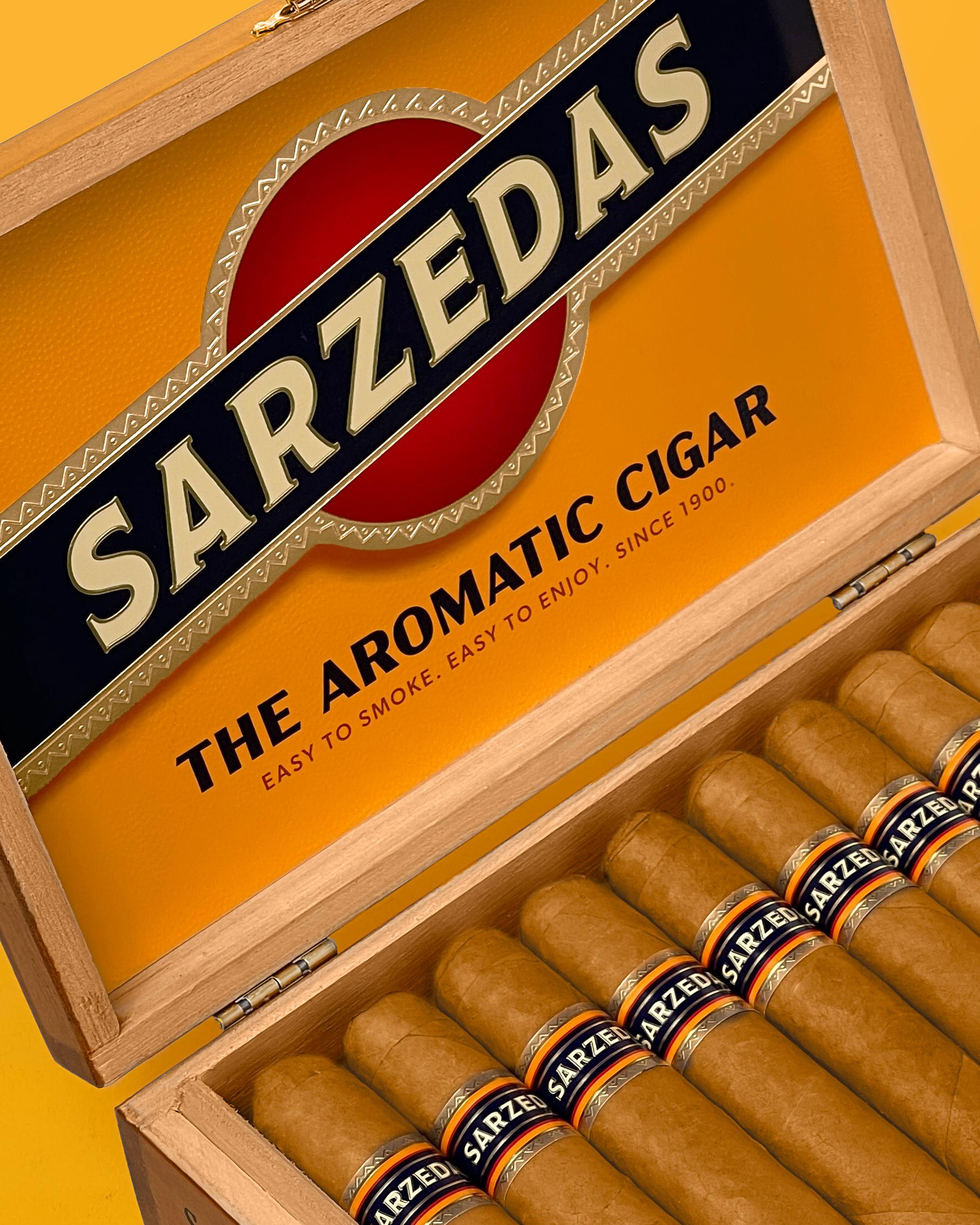
Sarzedas cigars are rolled in four sizes, a 6” x 50 toro, a 4.75” x 52 robusto, a 7” x 48 Churchill, and a 5.5” x 43 corona. They were blended by Rich Dolak, J.C. Newman’s longtime Vice President of Operations who has blending the cigars with the Newmans for 29 years. Sarzedas features a silky smooth Ecuadorian Shade wrapper, and binder and filler tobaccos from the Dominican Republic and Nicaragua. J.C. Newman will set the suggested retail price when Sarzedas is ready to ship this summer but expects it to be between $8 and $10 per cigar.
|
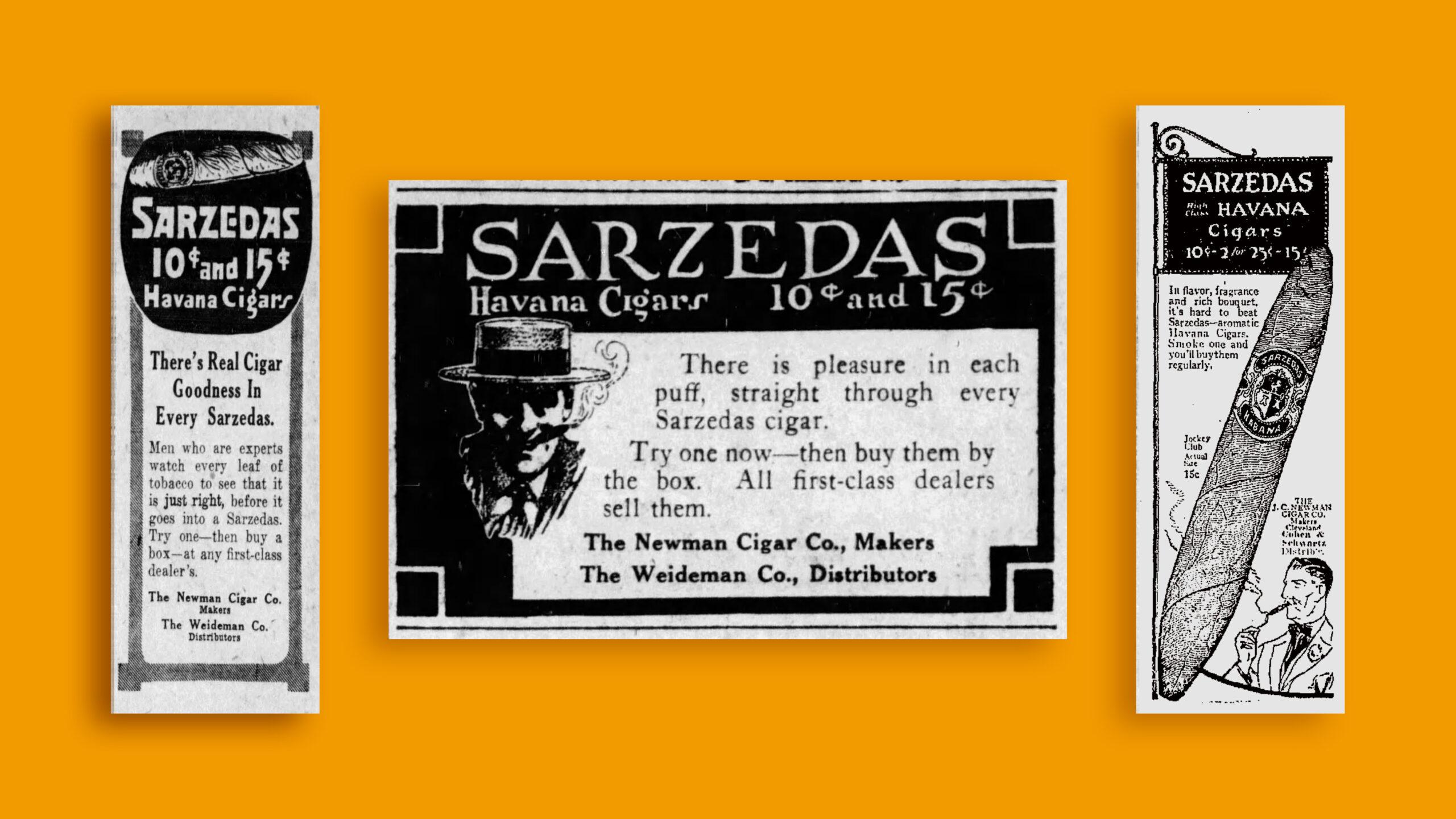
“Sarzedas is a fun, flavorful cigar that everyone can enjoy,” said Newman. The Sarzedas display at J.C. Newman’s booth will feature a vintage Sarzeda cigar box, a 100-year-old Sarzedas ashtrays, and Sarzedas newspaper ads from the early 1900s. |
J.C. Newman Introduces Sarzedas, a New Nicaraguan Brand
J.C. Newman Ships The El Reloj Collection
J.C. Newman ships the el reloj collection, a 2024 taa exclusive This new limited edition box set includes the first release of angel cuesta shade and tampa smokers. Tampa, Fla. – Today, J.C. Newman Cigar Co. is shipping The El Reloj Collection to Tobacconist...
J.C. Newman Introduces The Troublemaker
J.C. Newman Cigar Co. Introduces The Troublemaker This soft perfecto is the newest size in the Diamond Crown Julius Caeser brand of luxury cigars. J.C. Newman Cigar Co. introduces The Troublemaker, a new size to its top-selling Diamond Crown Julius Caeser brand...